As a by-product in the paper industry or as a main component for the production of various binders or fillers, the importance of lignin has continued to increase in the last few years. Hosokawa Solids has many years of experience and expertise in the field of conveying flammable and explosive bulk materials and therefore is the perfect partner for lignin applications.
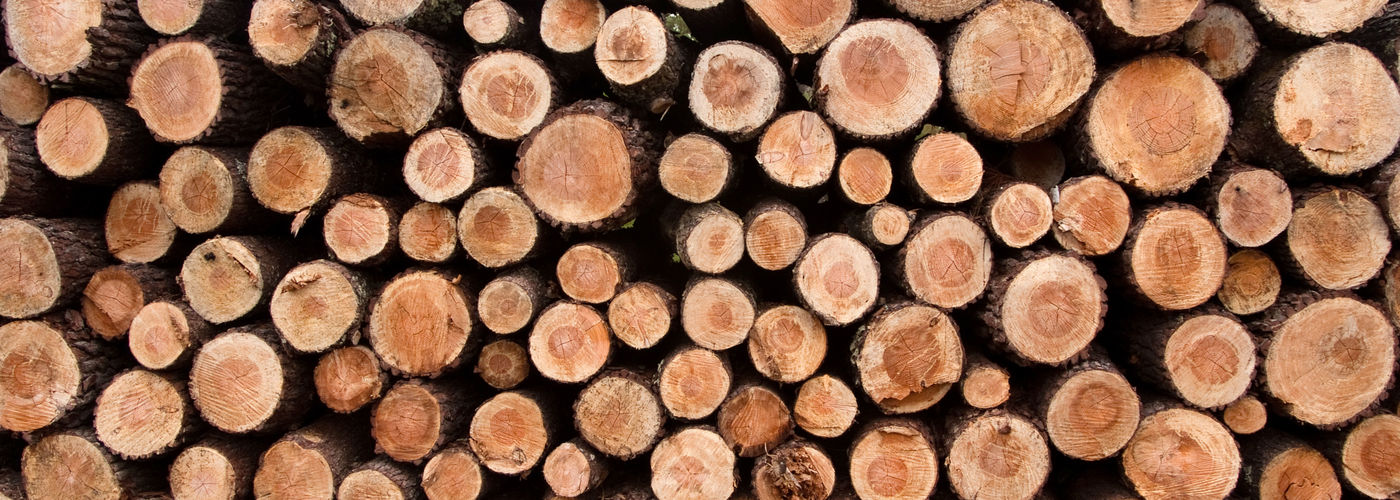
Fibenol: Extraction, storage and removal of lignin
From process consulting to turnkey systems„In this project, we worked with the customer to gain a foothold in what was previously a new area for all of us. We were able to convince the customer with our solution and complete the project to their satisfaction.“
Katalin Orth, Senior Sales Manager at Hosokawa Solids Solutions
What is lignin?
Renewable raw material with versatile propertiesLignin is an organic polymer and, alongside cellulose and hemicellulose, a component in wood. Here it has an impact on the lignification of the cell and the compressive strength and durability of the plant tissue. Overall lignin accounts for around 20 to 30 percent of the dry matter of ligneous plants. Previously, this natural raw material was regarded as a by-product produced during the manufacture of pulp or bioethanol and has scarcely been used industrially to date. In fact, lignin is versatile and can actually be used for the various end products – from batteries to cosmetics.
Lignin project with Fibenol
A few years ago, Hosokawa Solids successfully completed its first project for its customer Fibenol in Estonia and accompanied them from detailed product investigations through comprehensive pre-engineering to the successful implementation of the project.
- industry: production of wood-based raw materials
- goal: replacing fossil materials with wood-based materials
- solution: plant for processing lignin
The plant converts wood (4 tons of dry matter per hour) into C5 and C6 wood sugars and Lignin. C5 and C6 wood sugars can be used to produce bioethanol, bio-based polymers and for fermentation.
- product receiving of dried lignin from the on-site dryer
- pneumatic pressure conveying with rotary piston blower with three-bladed pistons and integrated pulsation reduction
- dosing into the conveyor line using a blow-through valve
- pneumatic conveying line over 40 m in silos, product distribution with rotary tube diverter
- professional design of the silos with bursting discs, CO-measurement mg/m3 air in the silo head space and temperature monitoring over the entire height of the silo cylinder
- filling with complete big bag filling including pallet dispenser and roller conveyors, with movable big bag docking and calibratable big bag weighing
- integrated aspiration system for dust-free handling
- planning, delivery, assembly and commissioning: „Everything from one source”
Product | lignin |
---|---|
Bulk density | 0.43-0.55 kg/dm |
Product temperature | max. 80 °C |
ATEX zone | 20 inside/22 outside |
Delivery capacity | 1.500 kg/h |
Conveyor line | 48 m, 7 bows 90 ° |
Filling performance | max. 10 big bags per hour |
The discharge of powdered and ground lignin presents the material handling system with particular challenges due to its “shooting” flow properties. To solve this problem, specific designed rotary valves are installed at the silo outlet before the inlet dosing screw.
Finished lignin products are filled into big bags. This is combined with weighing and dosing in order to be able to record and reproduce the filled amount. The selected rotary valves and dosing screw are controlled by frequency converters to enable rough and fine dosing.
Lignin is a material that required thorough handling procedures to ensure safety during processing. The following three measures are recommended to protect personnel and the plant.
Based on the project, further orders for handling lignin have been won, which are currently being processed. Due to the versatile application possibilities of lignin, Hosokawa Solids is faced with new challenges, in this case “wet lignin” is to be emptied from big bags, conveyed with a pneumatic transmitter and transported to several receiving containers using Puls Pneu Conveying. Thanks to the experience and know-how already gained in the project, this challenge will also be mastered.
Nice to know for your lignin transport
While simple thin-phase conveying is possible with lignin powder, the sensitive granulated lignin must be conveyed more gently at the end of the process. This is done by using our pneumatic Puls Pneu conveying or Step Pneu conveying.
In the production process for granulated lignin, it is necessary to stockpile raw materials, buffer intermediate products and store end products. The subsystems must meet bulk material and process requirements. For example, a mass flow silo with suitable discharge aids is required for storing granulated lignin.
Explore more: Lignin | Hosokawa Solids | All Case Studies