Calcium Carbonate (GCC) produced from chalk, limestone, calcite or marble have developed in recent years from just being a simple cheap filler to highest quality functional additives. GCC is used as dry powder or slurry in many industrial applications for plastic, paint, rubber, sealants or paper. Furthermore, a strong trend and shift to significantly finer grades is clearly observed in the range of finer than d97 < 10 μm to d97 < 1.6 μm. Special designed very steep particle size distributions as an functional additive for the production of breathable film in the hygiene field (for example baby diapers) or building material represent a further demanding challenge. GCC as an additive in almost all polymers must be subjected to a surface treatment, known as coating by means of technical stearic acid. In recent years the demand for highest coating GCC quality increased significantly. Highest hydrophobicity, few ppm residues in the upper size area of the particle size distribution, best 100% coating grade are required here. These demanding requirements are already met worldwide with Hosokawa Alpine equipment. For standard GCC fillers in the range d97 = 8 - 45 μm, a whole range of grinding / classifying processes are available with the focus on the lowest possible specific energy consumption.
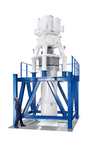